Tool service from professionals for professionals
Are you not only looking for great riveting and screwdriving solutions, but also want fast and reliable service solutions for your tools and machines from HST? We won't leave you out in the cold here either. Thanks to our effective and comprehensive tool service, you can also get damaged machines or tools back into use quickly.
To keep your productivity at a consistently high level, we also offer preventive service solutions, which are important for a long service life and the long-term usability of your tools.
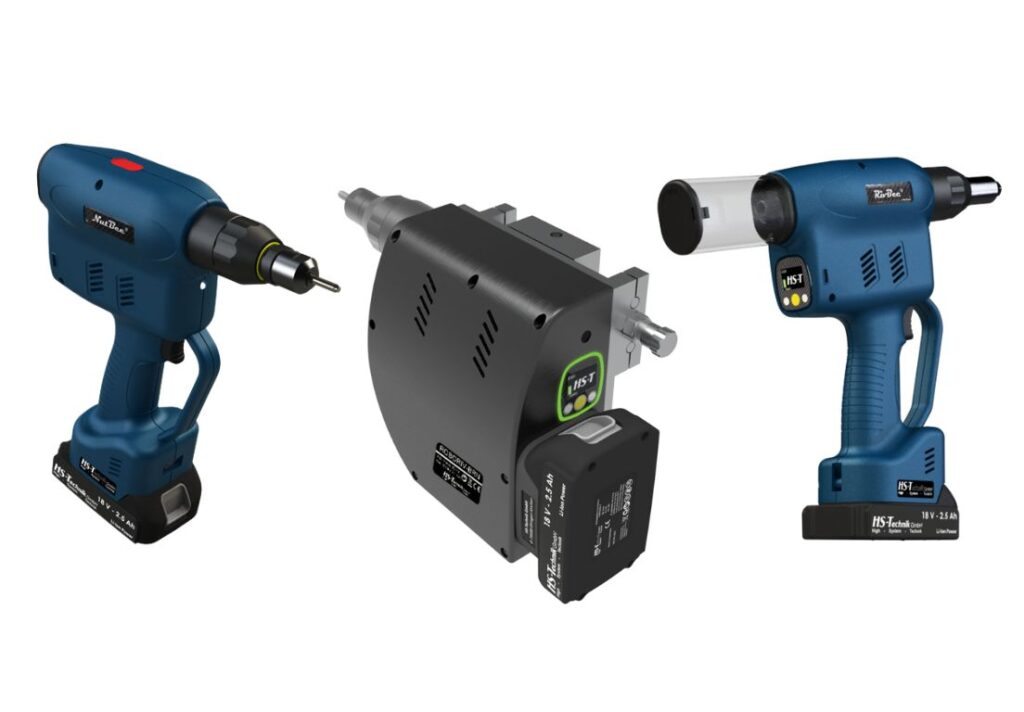
We offer you these services
1
Preventive maintenance
2
Repairs if required
3
Machine capability test
Since 1986, we have been offering you, our customers, a comprehensive and first-class service for the tools and machine tools purchased from our range. To ensure the high quality of our services, our qualified service technicians must always be up to date with the latest technology.
Further training and continuous development of our own skills are therefore part of our mission statement in our service team. Your advantage? In addition to the manufacture and commissioning of first-class tools and machines, we also offer you outstanding services in the areas of maintenance and repair of our products at a fair and transparent price.
If your tools require extensive repairs, our service technicians will also come to your company to carry out the necessary work directly on site.
Good to know...
High-quality machine tools from HS-Technik are not worth their price because of our label or our brand. But because of the excellent workmanship and the high-quality individual parts that are processed here.
To ensure that your tools can continue to deliver high quality in your daily work, you need original spare parts in the event of a repair or maintenance-related replacement of parts. As we know how durable our products are, we offer the right original spare parts for repairs or maintenance even years after the end of production of individual models.
This is how our tool service works
We want to make sure that you can do a good job with your tools for as long as possible. Whether you're in manufacturing or any other industry, if you need a tool reconditioned by HST, simply follow these 5 steps:
Step 1
You fill out our RMA form on our website
Step 2
Print out the form and send it together with the tool to the following address in Germany:
HS-Technik GmbH, attn. Repaircenter, Im Martelacker 14, 79588 Efringen-Kirchen
Step 3
Once we have received your tool, our service technicians will check your request. You will receive a cost estimate before the work begins.
Step 4
You check our cost estimate and give your approval for the necessary repairs.
Step 5
We will repair your tool and deliver the fully functional tool back to you.
Reliable repair instead of expensive replacement
Often, drives, controls or other wear parts of your tools do not even need to be replaced - quite often, repairing the defective parts would suffice. But even if a replacement is unavoidable, we offer our customers a service that is as reliable as it is fast.
As we have spare parts for all common machines in our range in stock, we can usually return the devices you send in for repair within 48 hours.
Use our repair support forms to download
Download and complete our repair or support form directly here:
RMA form
In order to process your repair as quickly as possible, please fill out this form completely and send it to us before sending in the repair.
Above all, it is important to send us a detailed description of the fault, preferably with a picture or video. Please avoid error descriptions such as "defective" or "no function".
A separate form must be created for each tool. Please complete this form and send it to repaircenter@hs-technik.com. You will then receive an RMA number from us, which you must enclose with the repair so that we can assign it correctly.
Please send the goods with the printed form to:
HS-Technik GmbH
Im Martelacker 12
79588 Efringen-Kirchen
Please note: Defective batteries may not be returned and must be disposed of by the customer.
Support Sheet
In order to be able to provide you with comprehensive support as quickly as possible, please send us the completed HST Service Sheet.
Service/ MFU form
In order to process your request for a service or MFU as quickly as possible, please fill out this form completely and send it to us before sending in the tool.
A separate form must be created for each tool. Please complete this form and send it to repaircenter@hs-technik.com. You will then receive an RMA number from us, which you must enclose with the tool so that we can assign it correctly.
Please send the goods with the completed form to:
HS-Technik GmbH
Im Martelacker 12
79588 Efringen-Kirchen
Please note: Defective batteries may not be returned and must be disposed of by the customer.
If you have any questions, please contact our service hotline directly:
from 07:30 to 17:00: 07628 9111 - 0
You can also submit your repair request by telephone here
Please send repair requests by e-mail to repaircenter@hst.group
FAQ - Frequently asked questions and answers
How do I access the setup menu to activate manual mode?
Press and hold the yellow button or remove the batteries. Also press and hold the start button while pushing it up.
How do I adjust the counterholder on the HT series?
Loosen and remove the torsion spring, then remove the counterholder and replace it on the multi-tooth in the desired direction, not forgetting the torsion spring.
Press and hold the yellow button or remove the batteries. Also press and hold the start button while pushing them on.
Loosen and remove the torsion spring, then remove the counterholder and fit it back onto the multi-tooth in the desired direction, not forgetting the torsion spring.
How do I set the force on the LF series?
Set the tool to setup mode by pressing the yellow button and switching to the "Program" menu item. Confirm this by pressing the start button. Then set the required force and confirm again by pressing the start button. Finally, exit setup mode.
How do I change the mouthpiece?
Remove the large union nut, take off the pull sleeve, remove the old mouthpiece and fit the new one. Then put on the pull sleeve and fit the large union nut.
How do I change the clamping jaws?
Remove the large union nut, remove the pull sleeve, pull the bayonet catch towards the tool and dismantle the clamping jaw housing. Remove the clamping jaws from the housing and replace them. Please ensure that you lubricate the new jaws and insert them into the jaw housing, reinsert the slider and spring and fit the bayonet catch. Finally, fit the pull sleeve and fit the large union nut.
How do I change the tension unit to a longer version?
First remove the large union nut and remove the tension sleeve. Then remove the tension unit using an open-end wrench SW14 and replace it with the desired length. Finally, fit the new tension unit, attach the tension sleeve and fit the large union nut.
Where can I get the password list?
Please contact the responsible contact person or the head office.
How do I install the device driver? Please download the driver from the website
, open the device manager on the end device (administrator rights required), select an unidentifiable USB device, right-click to search for current drivers (administrator rights required), select the driver from the download, restart the end device if necessary.
Where can I get the latest version of the Tool Manager?
Click here to download
The MFU / service is due, where should I send the tool?
Please fill out our RMA / service form and send the tool to: HS-Technik GmbH, Im Martelacker 12, 79588 Efringen-Kirchen.
Will I receive a replacement tool for the duration of the service / MFU?
Unfortunately, we cannot provide replacement or exchange tools. An emergency strategy in the event of a tool failure or service must be defined by the user.
How long does the service / MFU take?
The duration depends on the current workload of our service department.
The duration depends on the current workload of our service department.
Where can I find the list of your worldwide sales partners?
We regret that we cannot show the list for reasons of confidentiality. Please send us an e-mail to info@hs-technik.com and we will put you in touch with our partner in your country.
What can I do if the HST Tool Manager does not recognize my tool?
Check the USB cable, try a new or different cable. Check that you are using the latest version of the HST Tool Manager. Click here to download. Try connecting the device to another computer.
We regret that we cannot show the list for confidentiality reasons.
Please send us an email to info@hst.group and we will put you in touch with our partner in your country.